The IoT horizon for Asia’s producers past 2022 – Cyber Tech
The Web of Issues (IoT) has been round for years however solely within the current decade has its prominence moved up the notice chain following two important occasions: improvement round sensible options supported by sensors, units and applied sciences that kind a part of the IoT ecosystem.
The second, and arguably extra dramatic, are the practically persistent cyberattacks in opposition to personal companies and the continued operation of crucial infrastructure. Almost all industries are unable to flee unscathed from these assaults.
IoT adoption in manufacturing
Particular to Asia’s manufacturing sector, IDC is projecting continued progress within the integration of IoT applied sciences into the area’s manufacturing sector.
IDC estimates that in 2020, US$83.4 billion was spent on IoT know-how by producers in Asia/Pacific (excluding Japan) with discrete manufacturing accounting for 60% of spend. Course of manufacturing spent greater than US$33 billion in the identical yr.
By 2025, IDC expects discrete producers will ship US$88.7 billion in comparison with US$51.9 billion amongst course of producers. The analyst says producers can revenue drastically from retrofitting sensible sensors to previous tools due to the insights they will receive about their tools
FutureIoT touched base with Piyush Singh, senior market Analyst for IoT Insights, IDC Asia/Pacific to debate how IoT is trending throughout the manufacturing sectors of Asia.
Producers, whether or not in course of or discrete, have used instrumentations to get suggestions and supply some management over the manufacturing line. How can a producer introduce IoT know-how with out disrupting the manufacturing line?
Piyush Singh: Industrial IoT makes use of a community of sensors to collect essential manufacturing knowledge, and cloud software program to rework this knowledge into insightful data about how properly industrial actions are run. The first use case for expenditure was operations, adopted by manufacturing asset administration, upkeep, and discipline service.
Supply: IDC Manufacturing Insights
A lot of the producers begin with pilot testing by upgrading the prevailing legacy machines with the implementation of varied {hardware} merchandise. Moreover, it’s true that changing a plant entails a prolonged interval of machine downtime.
When it comes to time, that is regularly unsustainable. On this regard, a refit operation analysis could be useful. Probably the most tough barrier to a retrofitting effort is {that a} legacy system has machine instruments from many manufacturing eras with numerous connection protocols.
Course of management have to be carried out manually by monitoring, sensing, estimating, and modifying the machine parameters as a result of lack of sensors and actuators.
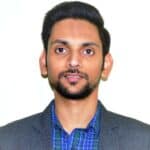
“Normally, in Asia, the retrofitting is accomplished in a phased method whereby one manufacturing line is taken for the upgradation to keep away from pointless downtime in manufacturing. As soon as the transformation of machines is accomplished in a single manufacturing line, later the retrofitting of different machines will probably be thought-about.”
Piyush Singh
Particular to producers in Asia, do you see data safety together with cyber safety, as a precedence over manufacturing? How has the notion/acceptance/angle in direction of safety modified over the past 5 years?
Piyush Singh: The fourth industrial revolution, typically often known as Trade 4.0, is the logical end result of the third revolution and is primarily centered on two key components: the Web of Issues and Companies (IoT) and Cyber-Bodily Techniques (CPS).
In Asia, retrofitting just isn’t solely the important thing idea of manufacturing unit automation. Cyber safety, knowledge safety, and enhanced knowledge privateness are all coated underneath one umbrella known as trade 4.0.
With the rising demand for IoT in numerous sectors, the demand for sturdy cyber safety can be the necessity of the hour. Spending on safety options and companies in Asia/Pacific is forecasted to exceed $31 billion in 2022, a rise of 15.5% from 2021 during which virtually $2 billion in safety spending could be underneath the discrete manufacturing part, in line with IDC’s newest Worldwide Safety Spending Information.
Regardless of headwinds akin to looming international recession, geopolitical conflicts, and rising inflation, investments in {hardware}, software program, and companies associated to cybersecurity are anticipated to achieve US$ 57.6 billion in 2026, with a CAGR (compound annual progress charge) of 16.4% for the interval of 2021-26.
China will proceed to be the area’s largest market, accounting for greater than 40% of whole Asia/Pacific* safety spending in 2022, with a five-year CAGR of 21.2% in the course of the forecast interval. This clearly showcases that the demand for safety infrastructure is rising within the Asia Pacific manufacturing sector.
If you happen to consider IoT integration within the manufacturing course of as a timeline, what IoT applied sciences do you see being deployed over time and what different applied sciences do you anticipate will comply with due to IoT?
Piyush Singh: A lot of the downtime and accidents are attributable to the wear and tear and tear of machines in lots of manufacturing vegetation. By virtualizing the plant and averting high-risk operator occurrences, the retrofitting aim is to make sure predictive upkeep purposes.
Distant monitoring and administration system, digital connectivity, cloud storage and robotic course of management are a few of the IoT retrofitting tendencies seen in manufacturing processes.
To determine and detect upcoming errors, Deep Studying algorithms and Digital Twin (DT) approaches is one thing which is getting used and have the tendency to develop exponentially in future. Synthetic neural networks (ANN) for detecting the instrument put on in a CNC machine after retrofitting is an idea which is in nice demand in lots of manufacturing vegetation.